All Under Control
Engine Management
Find your febi replacement part at partsfinder
Selected Products
All Under Control
with febi Engine Management Parts
In modern passenger cars, there is hardly any area that can get by without electronics.
The number of built-in electronic components is growing steadily and cars have become high-tech vehicles – safer, more comfortable and more environmentally friendly.
febi offers a dynamically growing assortment of replacement parts in the electronics and sensor area in OE-matching quality, suitable for various vehicle types.
We exclusively carry quality parts, for example, exhaust pressure sensors, EGR valves, ignition coils and air flow meters in our product range.
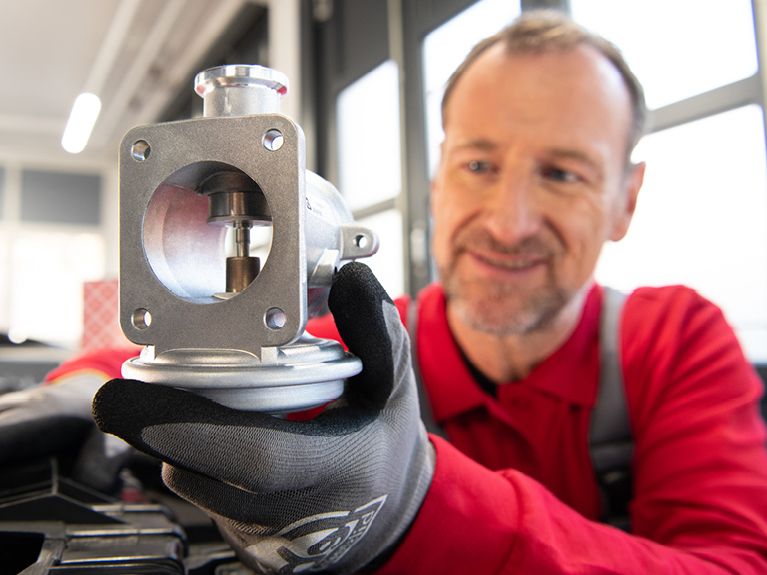
febi Engine Management Components
The Advantages at a Glance
Robust construction for flawless operation despite environmental influences
Tested according to strict quality standards
Optimal accuracy of fit for trouble-free repair
The requirements of vehicle manufacturers are met or exceeded
High-Tech in the Aftermarket
Sensors, and the technology they use, control and regulate engine management systems.
A sensor is a device able to acquire one or more physical characteristics such as temperature, position, movement, speed etc. and convert these into an electronically usable signal for the ECU to process.
Actuators are components which convert the electrical output signals from the ECU into physical quantities, to control the internal combustion engine for efficiency, economy and performance. This includes parts such as fuel injectors, ignition coils and electro pneumatic valves. Actuators send feedback to the ECU on variables such as position, power consumption and load to give greater control.
All Under Control
with febi Engine Management
- Range of 2,000+ Engine Sensors and Actuators
- Covering more than 60,000 European and Asian vehicle applications
- Dynamically growing range with 300+ articles per year
- OE-matching quality, tested and verified in-house
- febi is your No.1 in the Automotive Aftermarket for Engine Management replacement parts
EGR Valve
The purpose of the Exhaust Gas Recirculation (EGR) system is to reduce the emissions of oxides of nitrogen (NOx) from the engine’s exhaust.
There are two main types of EGR Valve. One is vacuum operated, which uses an electropneumatic pressure transducer, controlled by the ECU to open and close. The other is operated by a DC electric motor, or stepper motor. Both electronic and vacuum types are opened and closed subject to engine load.
- 150+ articles in range
- To fit more than 4,600 European and Asian applications
- Covering 70+ million passenger cars worldwide
Pressure Sensor
The Manifold Absolute Pressure sensor (MAP sensor) measures the pressure in the inlet manifold, providing instant manifold pressure information to the engine’s electronic control unit (ECU). The data from the MAP sensor is used to calculate air density and determine the engine’s air mass flow rate.
The data from this sensor can be used for diagnostic purposes as it measures the throttle and turbo performance, as well as to diagnose unmetered air leaks in the inlet manifold.
- 180+ articles in range
- To fit more than 5,000 European and Asian applications
- Covering 41+ million passenger cars worldwide
Crankshaft & Camshaft Sensor
These sensors measure the speed and position of the cam and crankshaft. Their signal is processed by the engine management ECU to improve the accuracy of the ignition and fuel timing.
The two main technologies used in these sensors are typically of a hall or inductive type. The operations of these sensors are fundamentally similar.
- 300+ articles in range
- To fit more than 25,000 European and Asian applications
- Covering 380+ million passenger cars worldwide
Air Mass / Air Flow Meter
Its signal is used to calculate the injected fuel quantity, and for regulating the exhaust gas recirculation in diesel engines.
There have been several different types of sensor used over the years, depending on the systems vehicle manufacturers used. The two main types are Air Flow Meters, or Air Mass Meters.
The description of Air Mass Sensors and Air Flow Meters are often used interchangeably. However this is incorrect as the Air Flow Meter only detects the air volume, whereas Air Mass Sensors are significantly more precise because temperature and pressure are also taken into account.
- Over 100+ articles in range
- To fit more than 12,000 European and Asian applications
- Covering 95+ million passenger cars worldwide
Ignition Coil
There are several design variations of the ignition coil and also the technology used is dependent on a variety of criteria.
Engine environment: temperature, installation, space allocated
Performance: Current supply requirements, ability to filter interference
- 130+ articles in range
- To fit more than 15,500 European and Asian applications
- Covering 190+ million passenger cars worldwide
Throttle Body
The engine management ECU has total responsibility for controlling the throttle valve inside the Throttle Body, with a DC motor to control the throttle valve angle. Feedback is then given to the ECU via a throttle position sensor. Together, these components make up the Electronic Throttle Control.
The throttle control also plays an important role in emissions reduction, particularly in direct injection petrol engines when switching between homogeneous or stratified modes, as well as to control fresh air for the EGR.
- 80+ articles in range
- To fit more than 3,200 European and Asian applications
- Covering 40+ million passenger cars worldwide
OE-Matching Quality by 100%
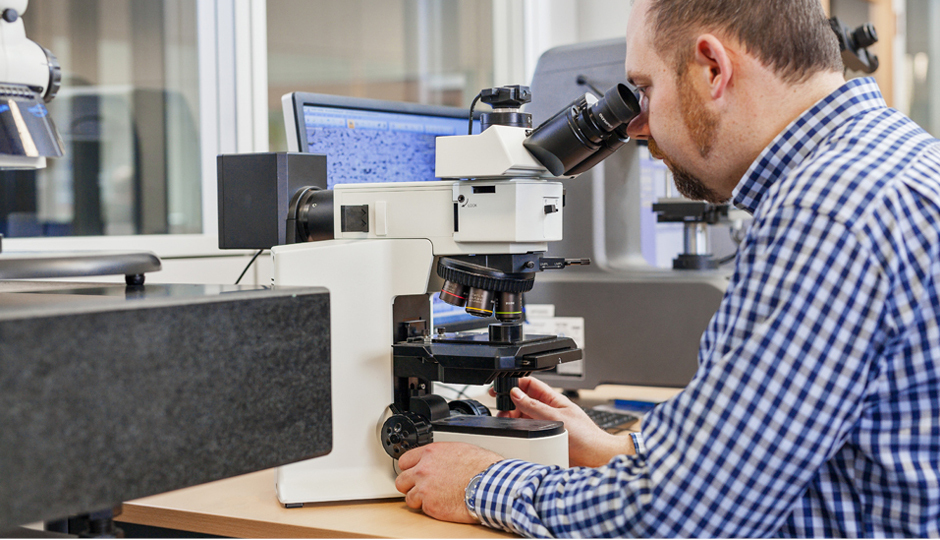
febi rests its reputation firmly on the quality of the products provided to the Automotive Aftermarket. Every febi part is submitted to intensive and regular quality checking with electrical components being no exception.
Every febi part has been designed and manufactured to meet OE standards and regular destructive and non-destructive testing ensures a continued supply of quality products.
You can be assured that all febi Engine Management components are manufactured to the highest standards and can be fitted to any vehicle without invalidating the vehicle manufacturer’s warranty.
Quality control is a crucial aspect of the febi process: for sensors and actuators, this inspection process includes checking circuit boards, resistors and capacitors for damage, and analysing the wiring for any issues. Additionally, the connection points of the circuit boards and the soldering of resistors and capacitors are checked.
Get the febi Newsletter